Case Study: Enhancing Energy Efficiency for a Local Manufacturing Plant
Introduction to the Challenge
In today's competitive market, energy efficiency is not just an option; it’s a necessity. With rising energy costs and increasing environmental concerns, industries are under immense pressure to optimize their energy consumption. This case study explores how a local manufacturing plant successfully enhanced its energy efficiency, leading to significant cost savings and reduced carbon footprint.
Understanding the Initial Scenario
The manufacturing plant in question was facing high energy bills, impacting its profitability. Initial assessments revealed that outdated equipment and inefficient processes were the primary culprits. The plant's management realized the need for a comprehensive energy audit to pinpoint areas of improvement.
After a thorough examination, it was evident that a strategic approach was essential. The plant's energy usage was analyzed across various operations, from machinery to lighting and HVAC systems. This data-driven approach formed the foundation for developing targeted solutions.
Implementing Energy Efficiency Measures
To address the identified issues, a series of measures were implemented:
- Upgrading Equipment: The plant invested in state-of-the-art machinery that consumes less energy and operates more efficiently.
- Optimizing Processes: Lean manufacturing techniques were adopted to minimize waste and streamline operations.
- Enhancing Insulation: Improving the insulation of buildings helped reduce the need for heating and cooling.
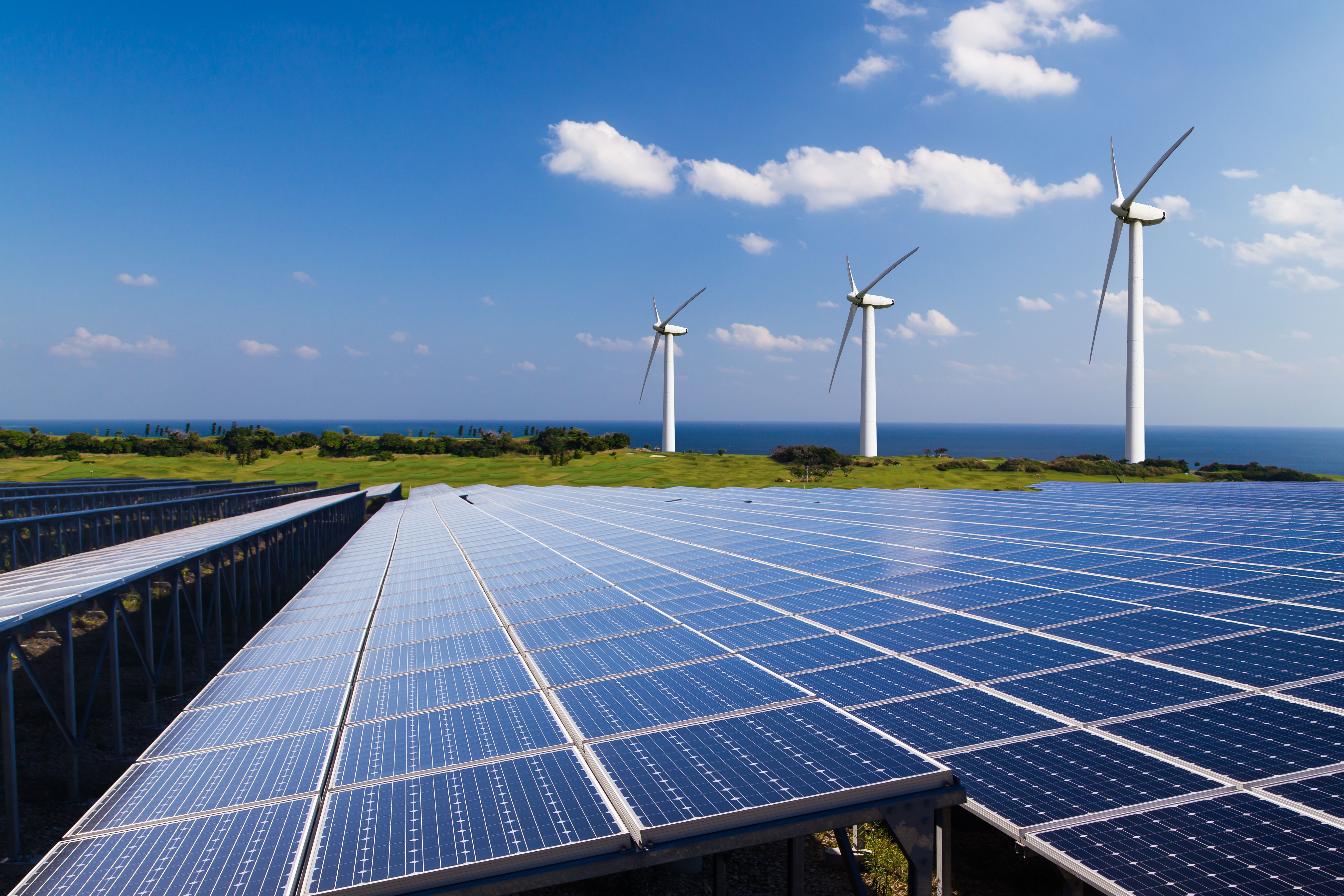
Monitoring and Evaluation
Post-implementation, continuous monitoring was crucial to assess the effectiveness of the changes. Advanced sensors and meters were installed to track real-time energy consumption. This not only helped in maintaining efficiency but also provided valuable insights for further improvements.
The data collected was analyzed periodically, allowing the management to make informed decisions. Adjustments were made as needed, ensuring that the plant maintained its energy-saving trajectory. Regular training sessions for employees also played a key role in sustaining these improvements.
Results Achieved
The results were remarkable. Within the first year, the plant reduced its energy consumption by 25%, leading to substantial cost savings. The enhanced efficiency also contributed to a 20% reduction in the plant's carbon emissions, aligning with global sustainability goals.
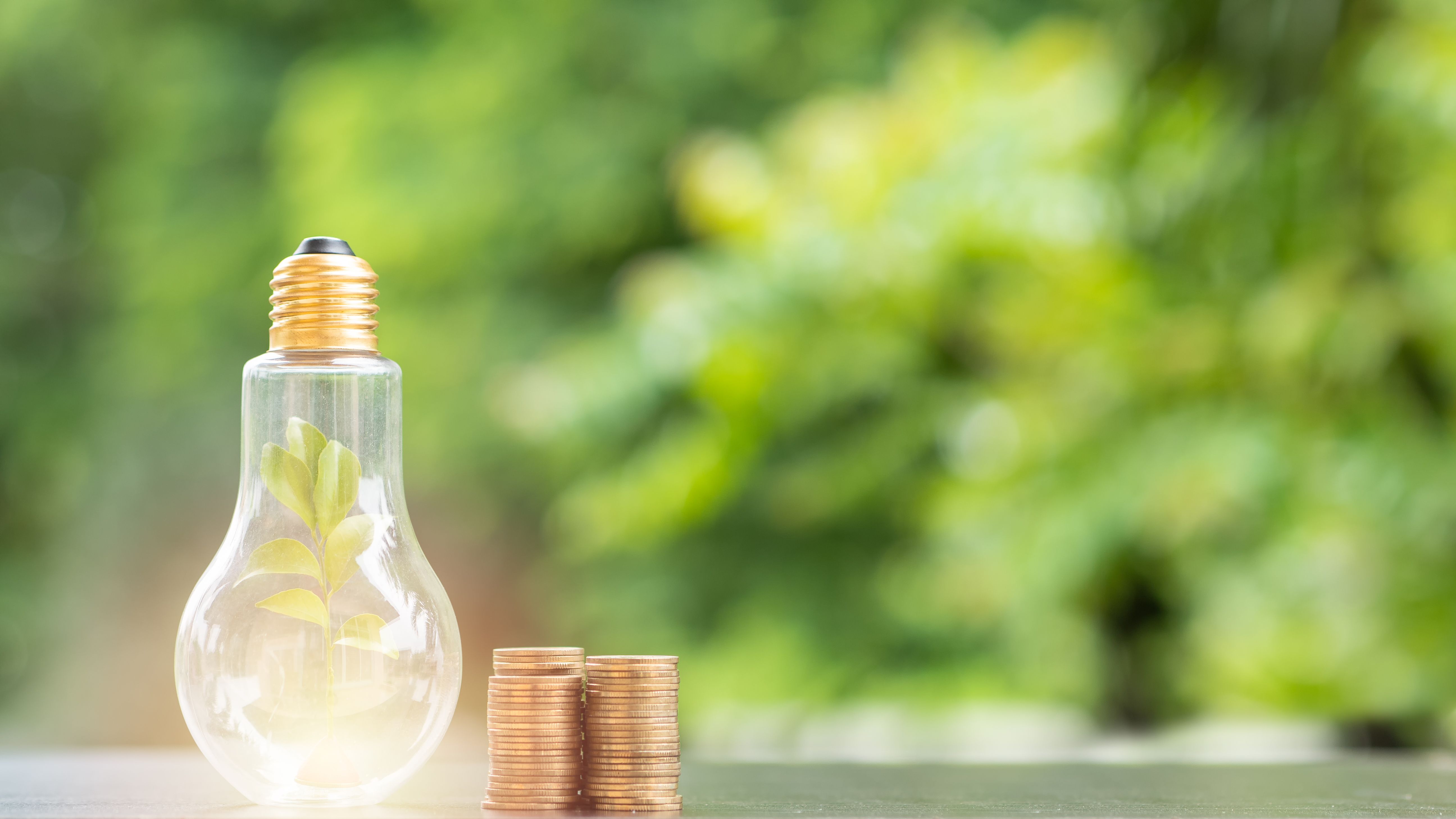
Moreover, the plant's commitment to sustainability improved its reputation among customers and stakeholders. It set an example within the industry, demonstrating that investing in energy efficiency can lead to both economic and environmental benefits.
Conclusion
This case study highlights the importance of proactive measures in enhancing energy efficiency. By upgrading equipment, optimizing processes, and embracing technology, the manufacturing plant not only cut costs but also contributed positively to environmental conservation.
For other businesses looking to follow suit, this case study serves as an inspiring blueprint. The journey towards energy efficiency is not just about reducing expenses but also about building a sustainable future for generations to come.